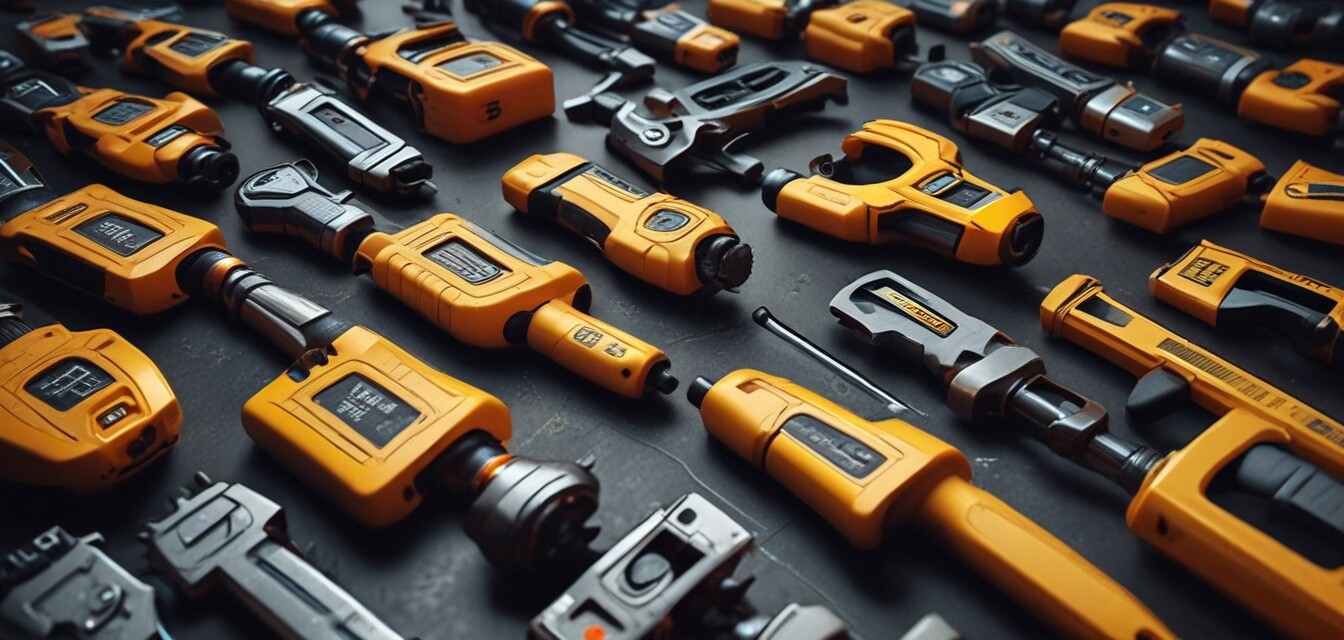
New Safety Standards in Power Tool Manufacturing
Key Takeaways
- The latest safety standards significantly impact power tool manufacturing.
- Manufacturers must comply with updated regulations by 2025.
- New technologies are being integrated to enhance safety features.
- Contractors and DIY enthusiasts benefit from improved tool performance and safety.
- Staying informed is crucial for making the best purchasing decisions.
The world of power tools continues to evolve as new safety standards emerge, particularly those set to take effect in 2025. These changes aim to enhance user safety, reduce injuries, and ensure tools meet higher manufacturing standards. In this article, we will explore the latest safety standards in the industry and what they mean for manufacturers and users alike.
Understanding the New Safety Standards
The power tool manufacturing sector is typically subject to rigorous safety standards, enforced by various regulatory bodies. The latest standards emphasize material safety, ergonomic design, and the performance of protective features. Here's a closer look at the key components of these standards:
Component | Description |
---|---|
Material Safety | Materials used in power tools must meet new health guidelines to minimize risks from toxic substances. |
Design Ergonomics | Tools should be designed to reduce strain and discomfort during use, accommodating a variety of user sizes and capabilities. |
Protective Features | Enhanced blade guards, automatic shut-off mechanisms, and warning systems are being required. |
Durability Testing | Tools must undergo more rigorous testing to ensure they can withstand stress under typical usage conditions. |
Why Are These Standards Important?
Safety standards play a critical role in protecting both users and manufacturers. Here are a few reasons why they are important:
- Reducing Injuries: Enhanced safety features lead to a decrease in workplace injuries related to tool misuse.
- Building Trust: When manufacturers adhere to safety standards, it instills confidence in consumers regarding the tools they use.
- Regulatory Compliance: Staying compliant helps manufacturers avoid legal penalties and build a reputable brand.
Impact on Power Tool Manufacturers
Manufacturers will face various challenges as they adjust to the new standards. Key impacts include:
Pros
- Opportunity to innovate with new technologies.
- Improved marketability due to compliance with safety standards.
- Potential for increased customer loyalty.
Cons
- Higher production costs due to advanced materials and technologies.
- Need for staff training to meet new manufacturing processes.
- Possible delays in product launches as adaptations occur.
What to Expect in 2025
As the deadline approaches, all eyes are on manufacturers to see how they will adapt. Expect to see:
- Innovative designs that prioritize user safety.
- Rapid adoption of smart technologies.
- Increased collaboration between manufacturers and safety regulatory agencies.
Staying Informed
For contractors and DIY enthusiasts, keeping up with the latest safety standards can aid in making informed choices when purchasing tools. You can explore more insights and resources about buying guides and take a look at the latest trends in power tools in our News and Trends section.
Conclusion
The advancements in safety standards for power tools are set to reshape the landscape of the industry in 2025. Not only do they promise to protect users, but they also encourage manufacturers to innovate and enhance the tools we rely on daily. By staying informed, you can ensure that you choose the safest and most effective tools for your projects.